News Story
UMD Scientists Achieve Ultrahigh-Temperature Melt Printing
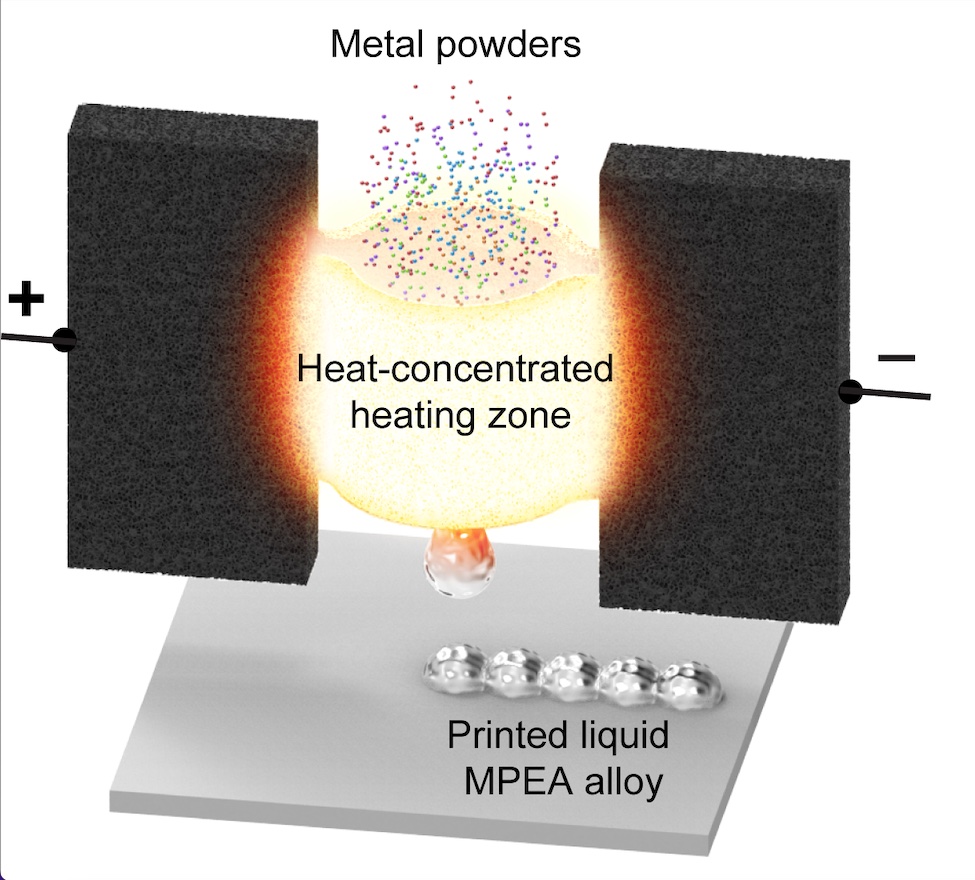
Multi-principal element alloys (MPEA) featuring three or more principal elements present in significant amounts display unique and extensively tunable properties due to their significantly expanded compositional design space. Three-dimensional (3D) printing is an emerging process with a great potential to fabricate geometrically complex MPEA structural products with favorable properties and performances. To achieve a high heating temperature for rapid multi-elemental melting/mixing during printing, focused high-energy sources (e.g., lasers, electron beam, electric arc) are commonly used to melt metal powders into dense products. While the temperature of these heating sources is sufficiently high to melt a wide range of elements, these approaches can only achieve a small-sized melt zone, which results in a highly uneven temperature distribution.
To overcome these problems, a University of Maryland research team led by Liangbing Hu, Herbert Rabin Distinguished Professor in the Department of Materials Science and Engineering (MSE) and director of the Center for Materials Innovation, designed a heat-concentrated heating zone to achieve rapid multi-elemental melting and uniform mixing for MPEA fabrication. The work was published in Nature Communications on November 7. Dr. Xizheng Wang, an MSE Assistant Research Scientist at UMD, served as the first author of the research paper.
In a typical fabrication process, multi-elemental metal powders are loaded into a high-temperature column zone that can be heated up to 3000 K via Joule heating. Based on heat transfer modeling, within milliseconds, the metal powders melt and mix into homogenous liquid alloy attributed to the sufficiently uniform high-temperature heating zone. The liquid alloy is then extruded from the heating zone and cools down at a rate of hundreds of K/s. Such rapid quenching is beneficial for achieving a homogenous multi-elemental chemical composition and microstructure with uniform grain size.
As a proof-of-concept demonstration, the team fabricated a single face-centered-cubic (FCC) phase NiFeCrCo MPEA featuring uniform elemental distribution, characterized by collaborators Prof. Wei Xiong’s group at the University of Pittsburgh and Dr. Chuan Liu at Northwestern University. At both the microscopic scale and nanoscale, they confirmed the uniform mixing of the multi-elemental metals.
The ultrahigh temperature melt printing platform features a concentrated high-temperature zone (up to 3000 K), enabling a broad range of metals to be used. It also demonstrates a relatively large heating zone with rapid and uniform melting and mixing of multiple metals into high-density bulk MPEA materials with uniform grain size; In addition, they have minimized loss of volatile elements during the rapid heating process. All the above advantages suggest the strong potential of the rapid melt printing platform as a heating source for MPEA 3D printing and suitability for high-throughput screening of different MPEA compositions for a wide range of applications.
Published November 10, 2022