News Story
UMD Scientists Convert Methane without Greenhouse Gas Emissions
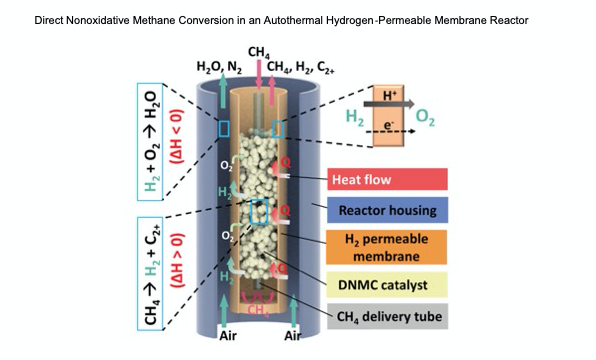
For the first time ever, scientists at the University of Maryland (UMD) have converted methane (CH4) into value added commodity chemicals such as ethylene and benzene with no greenhouse gas (GHG) production, a tremendous opportunity for both the chemical and natural gas industries.
Methane is one of the most abundant hydrocarbon resources used as a fuel worldwide. It is the principal component of natural gas, and while a major source of energy and economic growth, it is also a major environmental contaminant. Methane currently accounts for about 20% of the heating effects by all GHGs combined. Recent natural gas extraction methods have resulted in flaring and venting of gases which cause environmental harm and represent a lost opportunity for energy production.
Dr. Dongxia Liu, associate professor in chemical and biomolecular engineering (ChBE) at UMD, and Dr. Eric Wachsman, Director of the Maryland Energy Innovation Institute (MEI2) and William L. Crentz Centennial Chair in Energy Research at UMD, have developed a direct nonoxidative methane conversion (DNMC) membrane reactor which transforms CH4 to higher value hydrocarbons and hydrogen (H2) in a single step.
By coupling a DNMC-catalyst with an H2-permeable membrane, the team demonstrated an integrated membrane reactor that circumvents thermodynamic limitations leading to high CH4 conversion to value added chemicals in a single step without requiring conventional high cost and complicated separation schemes. Moreover, by using a simple air sweep on the other side of the membrane the team demonstrated that by oxidizing the permeated H2 to water all of the heat required for autothermal operation is achieved.
“This is a major breakthrough in the conversion of natural gas to major commodity chemicals not only in terms of the high yield achieved, but the fact that it is achieved with no GHG emissions. The only byproduct is water.” Said Wachsman.
This one-step membrane reactor is highly scalable, not only up for large scale chemical production but is a game changer as a small-scale modular gas-to-liquid reactor for stranded natural gas. Moreover, it provides a potential step change reduction in capital cost due to integration of catalysis and separation in a single unit while also dramatically increasing energy efficiency and eliminating GHG emissions.
The work was published in Advanced Energy Materials, and can be found at: https://doi.org/10.1002/aenm.202102782
Published October 27, 2021