News Story
Ion Storage Systems Says Its Ceramic Electrolyte Could Be a Gamechanger for Solid-State Batteries
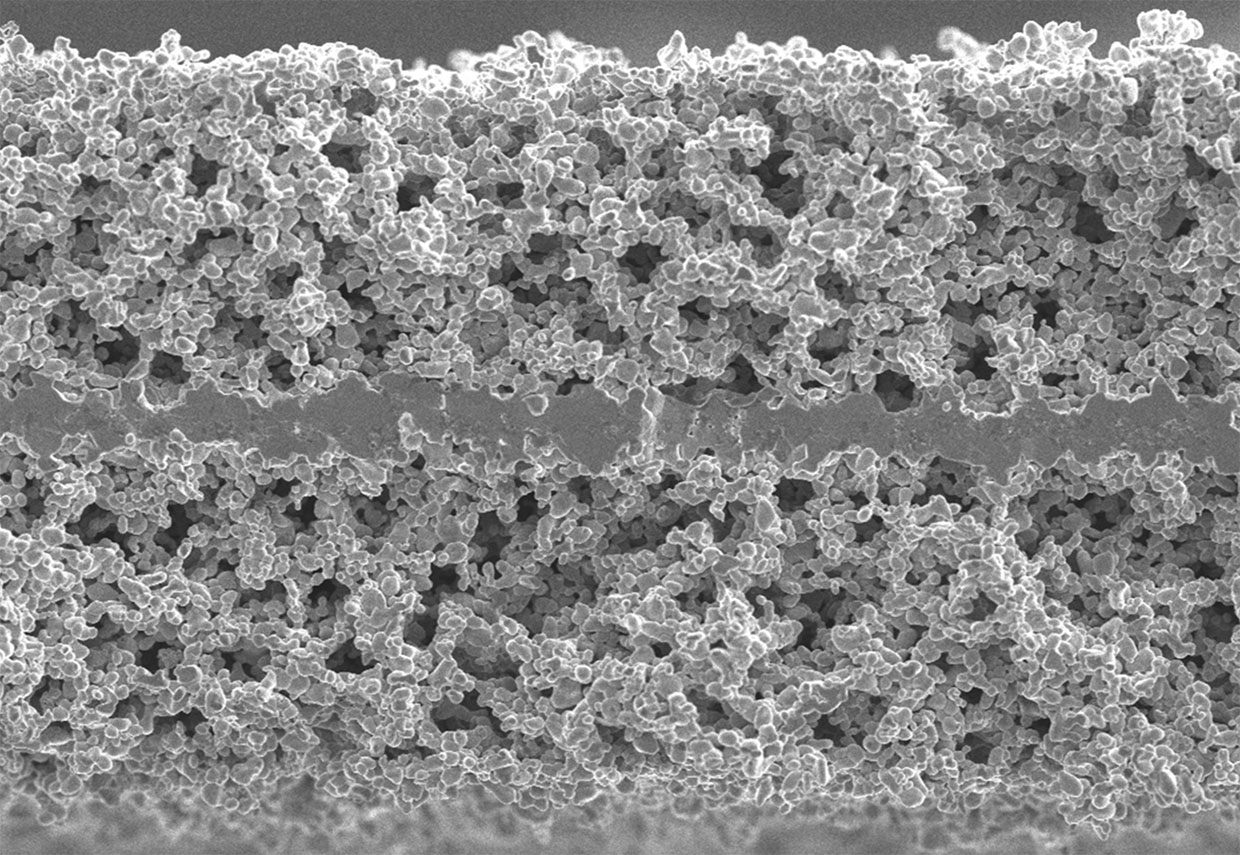
This electron microscope photo shows a thin, dense layer of a ceramic electrolyte that goes between two porous layers in a solid-state battery made by Ion Storage Systems.
Reposted from IEEE Spectrum
Author: Prachi Patel
For years, experts have predicted that solid-state batteries will be the next-generation technology for electric vehicles (EVs). These batteries promise to be safer by relying on a solid electrolyte instead of the flammable liquids used in today’s lithium-ion batteries. They could also last longer and weigh less, with a 10 times higher energy density, because they use a lithium metal anode instead of graphite.
Ford, Hyundai, Nissan, Toyota, and Volkswagen are all investing in solid-state battery research. And startups in the space abound.
But Eric Wachsman says his company, Ion Storage Systems, stands out for a few reasons. The company’s strong, dense ceramic electrolyte is only about 10 micrometers thick, which is the same thickness as the plastic separators used in today’s lithium-ion batteries, and it conducts lithium ions as well as current liquid electrolytes. And according to Wachsman, it overcomes two key issues with solid-state batteries: high electrolyte resistance and a low current capability.
The electrolyte has three layers. In the middle is a thin, dense layer of the lithium-oxide ceramic (with the chemical formula: Li7La3Zr2O12). On either side of that layer is a slightly thicker porous layer of ceramic with a superthin aluminum oxide coating that further reduces resistance.
Ceramics can be brittle. But the dense middle layer adds strength. It also makes the battery safer by blocking dendrites, which are tiny needles that can grow when lithium ions deposit on the anode unevenly, piercing the thin plastic separators in today’s cells and causing a hazardous short circuit. And the porous, aluminum oxide-coated layers allow lithium ions to move quickly into the electrolyte.
“It really comes down to the unique structure and interfacial treatments that allow us to get very low resistance,” Wachsman says. “High resistance has been the hang up for solid-state batteries.”
Because lithium ions flow exceptionally well between the electrodes and electrolyte, the battery has a high current density of 10 milliamps/cm2. And the near-zero risk of dendrites allows for batteries that charge quickly, “on the order of five to 10 minutes,” he says. “No one else has achieved that with solid electrolytes.”
Two other key metrics also seem competitive. The company’s prototype batteries have an energy density of about 300 Wh/kg, higher than the maximum of 250 Wh/kg that today’s commercial lithium-ion devices deliver.
Wachsman and his colleagues at the University of Maryland Energy Innovation Institute first reported the electrolyte structure in 2016. They make it with a conventional ceramic-manufacturing technique called tape casting, followed by sintering at high temperatures. He says the group chose oxide-based ceramics over sulfide-based ones, and over glass or plasticelectrolytes, because oxides work well over the largest voltage range, allowing lithium metal anodes and a wide variety of cathodes.
With research funding from the Department of Energy’s (DOE) Advanced Research Projects Agency-Energy and NASA, Wachsman launched the startup in 2015. The company is now making prototype batteries at its pilot production line, and has several customers lined up, he says.
At commercial scale, Wachsman says the cost of the batteries should meet the DOE’s goals of around $100/kWh that others in the industry are targeting. For now, the company is eyeing the unmanned aerial vehicle market because it can accommodate higher battery prices because of low-volume manufacturing at this early stage. “But we also have partnerships to develop batteries for the automotive and consumer electronics sector,” he says.
Published February 21, 2020